Stainless steel flat welded flange is a kind of application in the fluid piping system with low pressure grade, low pressure shock and not serious shock. Through the use of flat welding in the form of pipe connection, so in the welding assembly may cause some improper connection problems caused by leakage phenomenon. If that happens, we shouldn’t panic. First of all, the location of the leak should be found or the location of the gap between the flanges should be checked.
Steps to prevent flange leakage
Under normal circumstances, for the flange leakage problem, need to pay attention to the introduction of sealants, in addition to this there are many ways to remove the leak, according to our summary, to achieve effective plugging is very necessary.
In connection, under normal circumstances, the introduction of sealant should be carried out according to the ring shape, usually we can also be connected according to the flat welded flange in the case of injection, short flange connection, to avoid potential safety risks in the connection of the valve body, resulting in the leakage of flat welded flange.
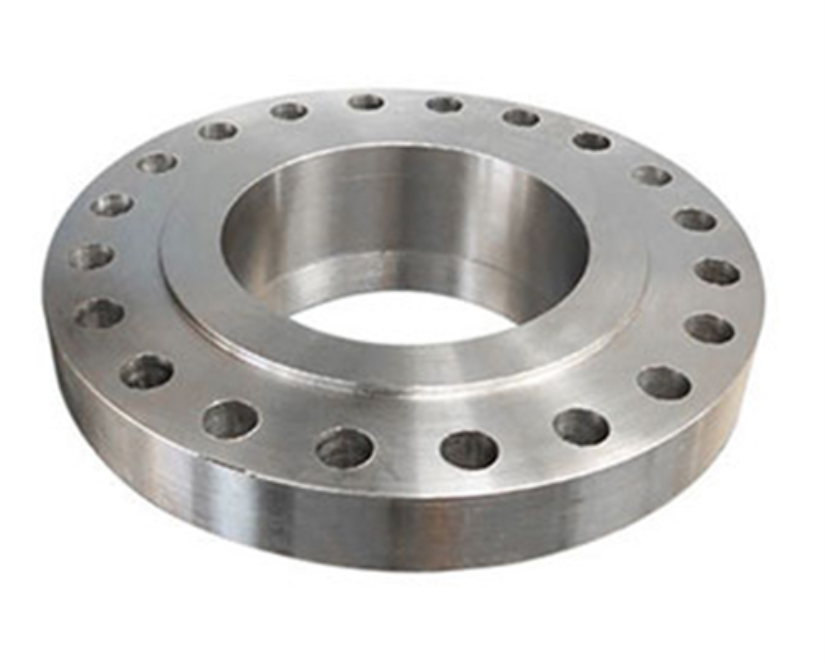
During the injection of the flange, the fixture should be moved as close as possible to the position of the small flange, or the tooth contact card should be used to limit the position
In the process of joint operation of flat welding flange, careful observation should be made to carry out reasonable arrangement. Stainless steel flat welded flange connection case, we also need to pay attention to
When connecting the flange with the cylinder, safety checks should be carried out on the cylinder end face with a ruler. During the measurement process, it is necessary to ensure that the inclined dimension of the end face does not exceed 15mm
The vertical degree of flange is measured with flange bending rule when the cylinder is connected with flat welded flange. These measures can effectively avoid the leakage of flat welded flange.
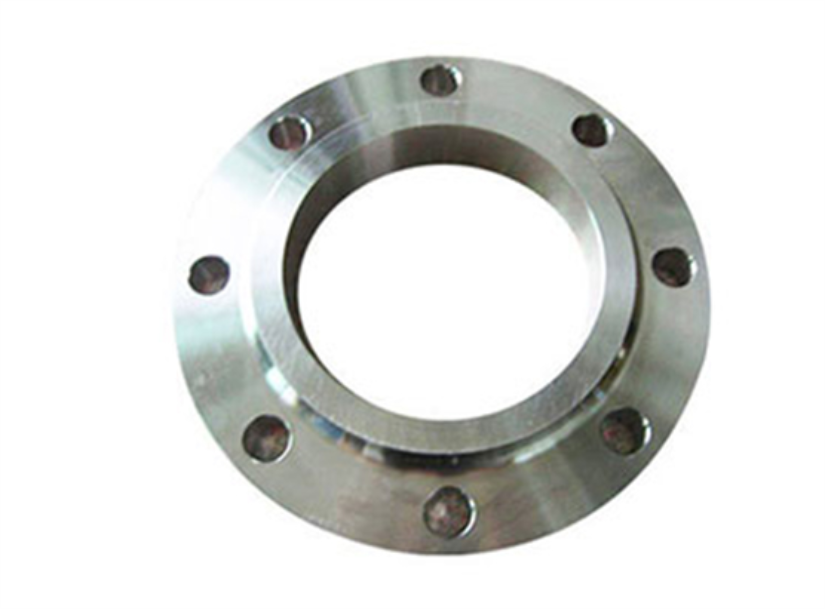
Precautions in welding
In order to avoid eye erosion due to the heating of the flange cover, the welding current should not be too large, less than 20% above and below the carbon steel electrode, the arc should not be too much, the interlayer fast cooling, and the narrow weld is more suitable.
When the electrode is used, it needs to be kept dry, titanium calcium type should be kept 150℃ dry for 1 hour, low a hydrogen type should be kept 200-250℃ dry for 1 hour, to avoid the electrode coating sticky oil and other dirt, in order to avoid increasing the carbon content of the weld and affecting the quality of the weldment.
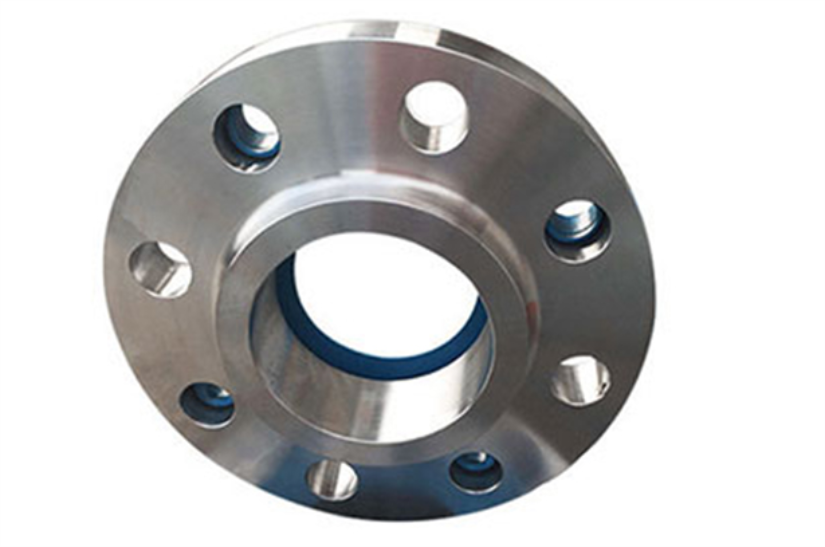
During the welding of flat welded flange fittings, carbides are precipitated by repeated heating, which reduces corrosion resistance and mechanical properties of products