Stainless steel flange processing steps are very important, but the meaning of quality seems to be more advantageous, manufacturers in the production process of stainless steel flange, do the next some common problems, so as to ensure the effect of the application.
Stainless steel flange processing points
For such materials as stainless steel, the most important thing is to maintain its surface clean, if it is etched after the surface of stainless steel will change shape, and not so smooth. Therefore, these items with etched stainless steel levels need to avoid processing. Whether acidic or alkaline gases or gases need to avoid the environment.
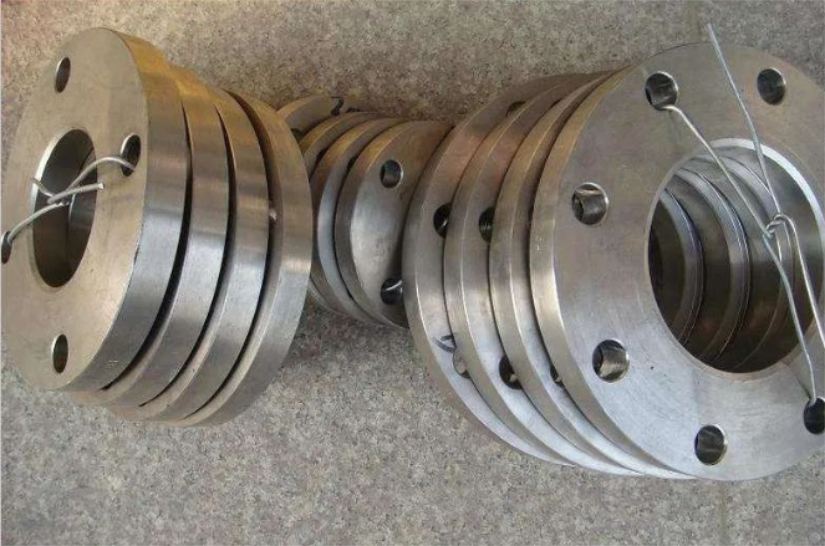
Select the combination flat pad of the flange, the effect of the flange on the access pipe is indeed larger, and the good assistant of the stainless steel flange in the combination application is the asbestos gasket. Materials like asbestos have good properties of their own, and it can also resist acidic substances
Either gas or gas can be well digested by asbestos, so it will not interfere with stainless steel. Naturally, in some special occasions will also be applied to other materials made of flat MATS, this time will be used and stainless steel has a complementary level of flat MATS.
There are different ways to access the pipe at the stage, these pipes are finer and can be immediately screwed into the stamped threaded flange, and some stainless steel flanges must face some pipelines with a greater burden, which must be applied to welding, so that it is more robust and reliable. The flange made of stainless steel is better or the use of welded joints, whether it is for heavy or small pipes.
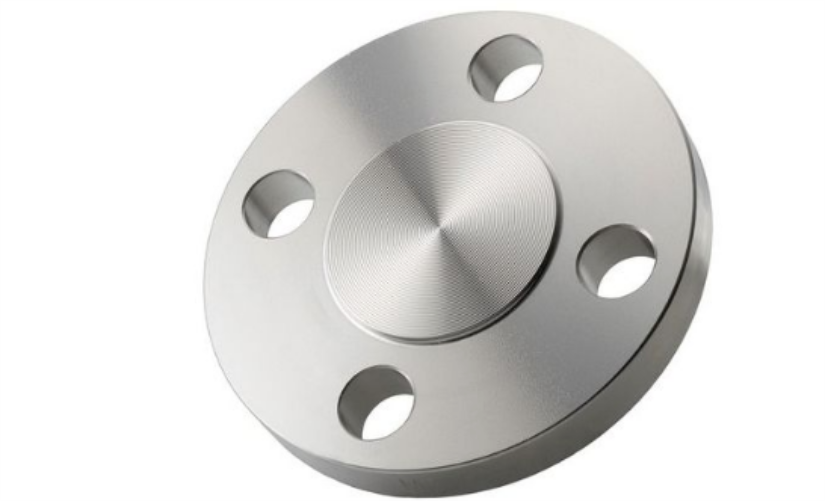
The aperture size of the stainless steel flange disc and the thickness of the flange are all related to whether the burden of the pipeline is large or small. Under normal circumstances, the greater the burden, the thickness of the stainless steel flange is also thick.
Maintenance stainless steel flange
When the French welding process is carried out, we are to prevent the lid from being corrosive, in fact, the current can not be too large during welding, so that it can cool down faster, which is also a better operation method.
In use, the most important thing we should use is to add some appropriate stability elements inside, so such elements can be very stable to a certain extent.
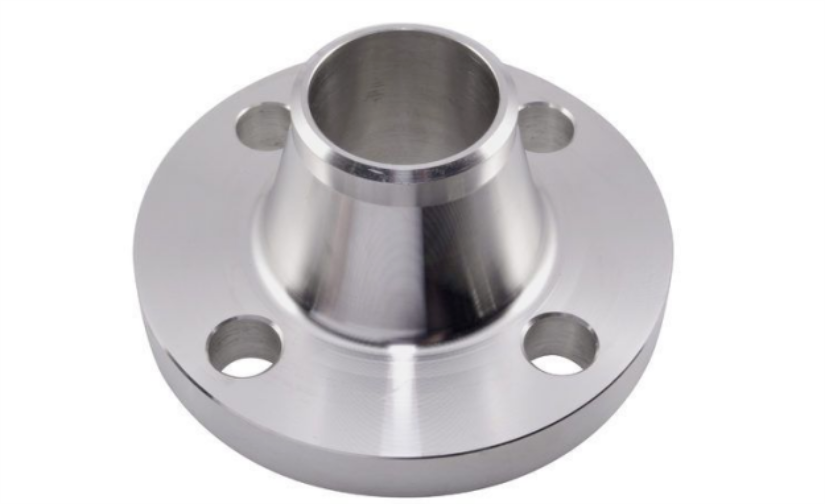
Welding will also produce a lot of problems, for example, if repeated, multiple heating, to a certain extent, it will reduce corrosion, such things are not easy
Many times what we see are some small details, if we can pay attention to these things, pay more attention, take more precautions, we can be well maintained to reduce the loss of goods.